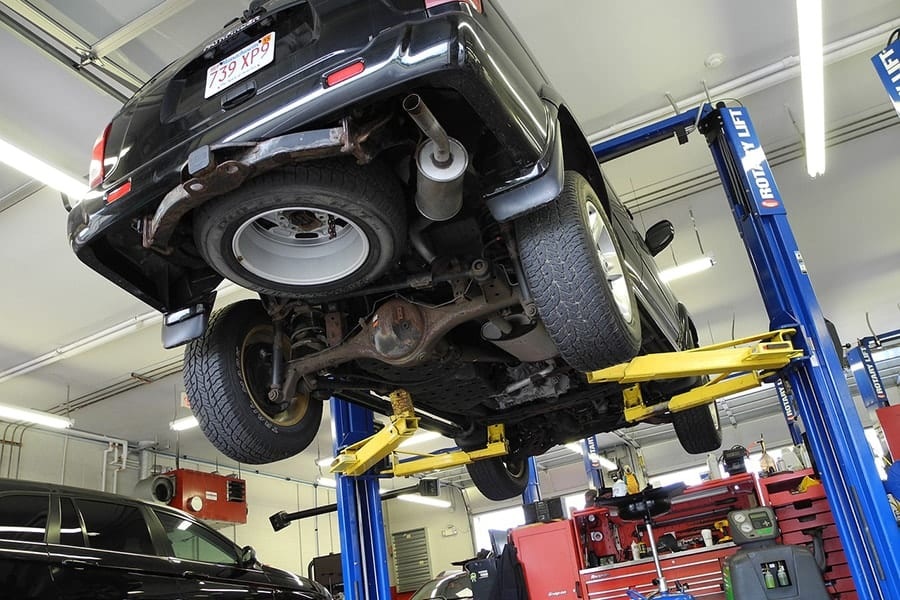
Wiring harnesses in vehicles are exposed to a variety of harsh conditions that can cause long-term damage. From extreme temperatures to moisture and debris, these elements can significantly impact the performance and lifespan of the wires. Insulation and shielding around the wiring harness play a crucial role in protecting the wires from these environmental factors. Proper insulation prevents moisture from causing corrosion, while shielding guards against heat, dirt, and physical wear. Without adequate protection, wires could degrade quickly, leading to electrical malfunctions or failures in vital vehicle systems.
Heat Resistance and Protection
One of the most significant threats to wiring harnesses is exposure to excessive heat, particularly in areas near the engine or exhaust. High temperatures can break down the plastic insulation, leading to short circuits or exposed wires. Insulation materials such as silicone or fiberglass provide heat resistance, ensuring the wires remain protected from engine heat or other high-temperature sources. This is crucial in maintaining the integrity of the harness and preventing failures in the vehicle’s electrical system, such as power loss, system shutdowns, or component damage.
Moisture Prevention and Corrosion Resistance
Moisture is another major threat to wiring harnesses, especially in regions with high humidity, rain, or snow. Without proper insulation, water can seep into the wiring, leading to corrosion and rust. This corrosion can degrade the wire’s performance, eventually causing electrical shorts or complete system failures. Insulated and shielded wiring harnesses are specifically designed to resist moisture, keeping the internal wires dry and free from corrosion. This protection extends the lifespan of the wiring and ensures the vehicle’s electrical components continue to function properly.
Physical Protection from Abrasion
Wiring harnesses are also at risk of physical damage from friction or impact. As the vehicle moves, vibrations and shifting can cause the wires to rub against surfaces or other components, wearing down the insulation. Shielding materials like braided steel or plastic coatings protect the wires from this abrasion. These materials act as a barrier, preventing direct contact with sharp edges, metal surfaces, or hot components. This protection helps avoid wire damage that could lead to intermittent electrical issues or complete system breakdowns. This is where the Auto Repair in Bakersfield, CA based services step in with the best solutions.
Preventing Electrical Interference
In addition to environmental and physical threats, wiring harnesses are vulnerable to electrical interference, especially in modern vehicles that rely on complex electrical systems. Shielding materials like foil or braided wire prevent electromagnetic interference (EMI) from affecting the signals traveling through the wires. EMI can disrupt the operation of sensitive systems such as the infotainment system, sensors, or safety features. Proper shielding ensures that these electrical systems remain unaffected by external electrical noise, promoting reliable vehicle performance.
In conclusion, insulation and shielding are essential for protecting the wiring harness from environmental, physical, and electrical damage. These protective layers extend the lifespan of the wiring, reduce the risk of failures, and ensure that your vehicle’s electrical systems function reliably. Regular inspections and maintenance are key to ensuring the harness remains in good condition, preventing costly repairs and system malfunctions.