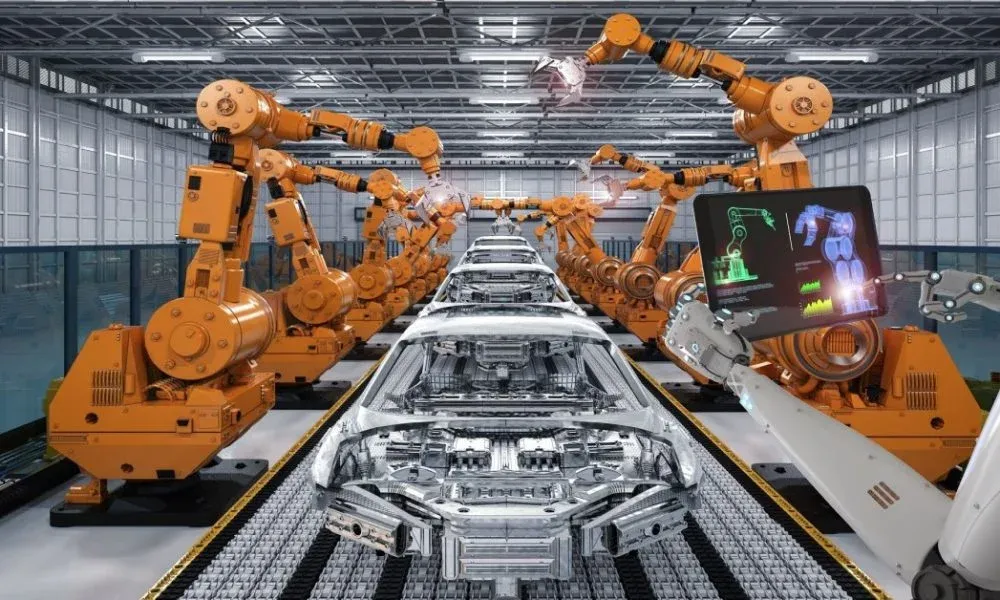
As electric vehicles (EVs) become more sophisticated, so does the technology behind their most essential components. One key area experiencing rapid transformation is the production of stator and rotor cores, where artificial intelligence (AI) is playing a groundbreaking role in increasing efficiency, precision, and scalability.
Transforming Core Production with Artificial Intelligence
In electric vehicle motors, stator and rotor cores are the central magnetic components responsible for converting electrical energy into mechanical motion. Their performance directly influences vehicle efficiency, range, and reliability. Traditionally, manufacturing these cores has required high-precision processes involving material selection, lamination, stamping, and stacking. While automation has been widely used, AI integration is now pushing production capabilities far beyond previous limits.
By facilitating adaptive control during production, predictive maintenance, and real-time decision-making, AI-powered systems are transforming core manufacturing. Each step of the process is optimized using machine learning algorithms that examine enormous volumes of sensor and production data. These systems can detect subtle deviations in materials, machine vibrations, and temperature changes—minimizing errors and reducing waste.
The result is a faster, smarter, and more consistent production environment where even microscopic defects can be identified and corrected instantly. This heightened level of quality assurance is critical in the competitive EV market, where motor performance is closely tied to energy efficiency and vehicle durability.
Precision Engineering Meets Smart Automation
Producing stator and rotor cores involves extremely tight tolerances. Even the slightest variation in thickness or alignment of laminations can compromise magnetic efficiency. With AI-driven quality inspection, manufacturers can now ensure that every sheet of steel meets exact design specifications.
Vision systems powered by deep learning are capable of inspecting thousands of laminations per hour. These AI tools detect irregularities such as edge burrs, surface defects, and misalignments that would be difficult for human inspectors or traditional machines to catch. When integrated with robotic handling systems, the entire process becomes seamless—from stamping and stacking to core assembly.
AI also assists in dynamic process adjustments. For example, if a coil used in the stator core shows signs of material fatigue during winding, AI systems can immediately adjust tension levels or alert operators to intervene. In addition to increasing operational efficiency, this prolongs the life of the manufacturing line’s tools and machinery.
Optimizing Material Use and Energy Efficiency
Another significant benefit of AI in manufacturing stator and rotor cores is material optimization. Electrical steel, often used for its superior magnetic properties, is a costly resource.AI algorithms can examine past production data to suggest material utilization plans that reduce waste and maximize cutting patterns.
Moreover, energy consumption across the production line is continuously monitored and optimized. AI systems track motor usage, press loads, and idle times, allowing facilities to reduce energy waste and improve environmental performance—critical for manufacturers looking to meet sustainability targets.
This level of control and resource efficiency also has implications for stator and rotor lamination processes. By reducing variability and energy consumption during lamination stacking and bonding, manufacturers can achieve higher yields and more durable cores, ultimately supporting the goals of high-performance EV motor production.
Global Impacts and Industry Adoption
The integration of AI into stator and rotor core production is not limited to large automakers. In order to remain competitive and satisfy growing demand, suppliers and specialist manufacturers worldwide are implementing these technologies. AI-enhanced facilities can scale more easily, handle higher product variability, and support custom designs for advanced EV platforms.
Companies like Gator Lamination have begun investing in intelligent manufacturing systems that combine traditional motor core engineering expertise with cutting-edge AI capabilities. By doing this, they put themselves in a position to lead EV innovation and provide customized solutions that satisfy the strictest requirements for effectiveness and quality.
AI also plays a key role in workforce development. Operators are now equipped with user-friendly interfaces that provide real-time feedback, guided maintenance instructions, and alerts based on AI predictions. This creates safer, more responsive working environments while upskilling the existing workforce.
Looking Ahead
The need for motors that are lighter, more efficient, and more powerful will increase rapidly as EVs continue to develop. AI-powered manufacturing of stator and rotor cores will remain a cornerstone of this progress—offering unmatched precision, quality, and scalability.
The combination of smart automation and advanced analytics is not just a trend but a defining shift in how motor cores are designed and produced for the next generation of electric vehicles.
Conclusion
AI is reshaping the way stator and rotor cores are manufactured, making production faster, smarter, and more reliable. As the electric vehicle industry accelerates, AI-driven innovation will ensure that core components meet the highest performance standards—powering the future of mobility.